

Creo sketch to gmsh generator#
Note that there is a difference the way CAD environment treats geometrical entities and the way mesh generator software use those information.
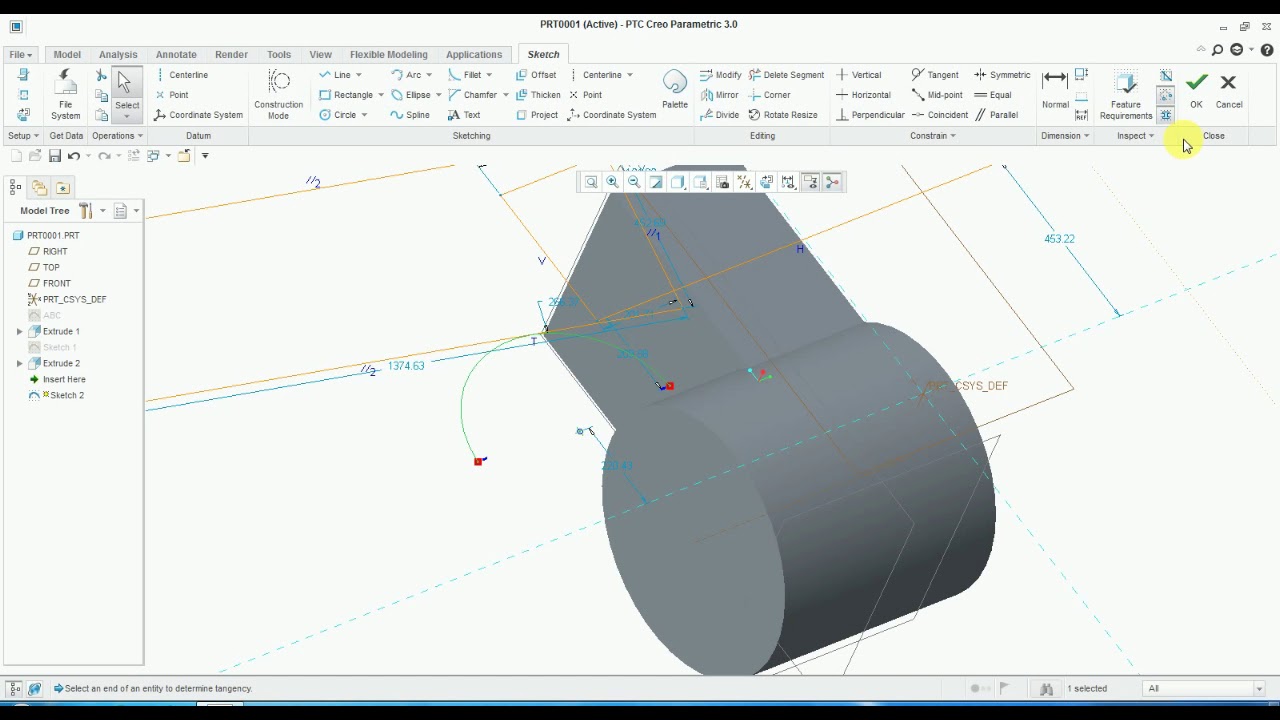
Some of the jargons associated with meshing are:
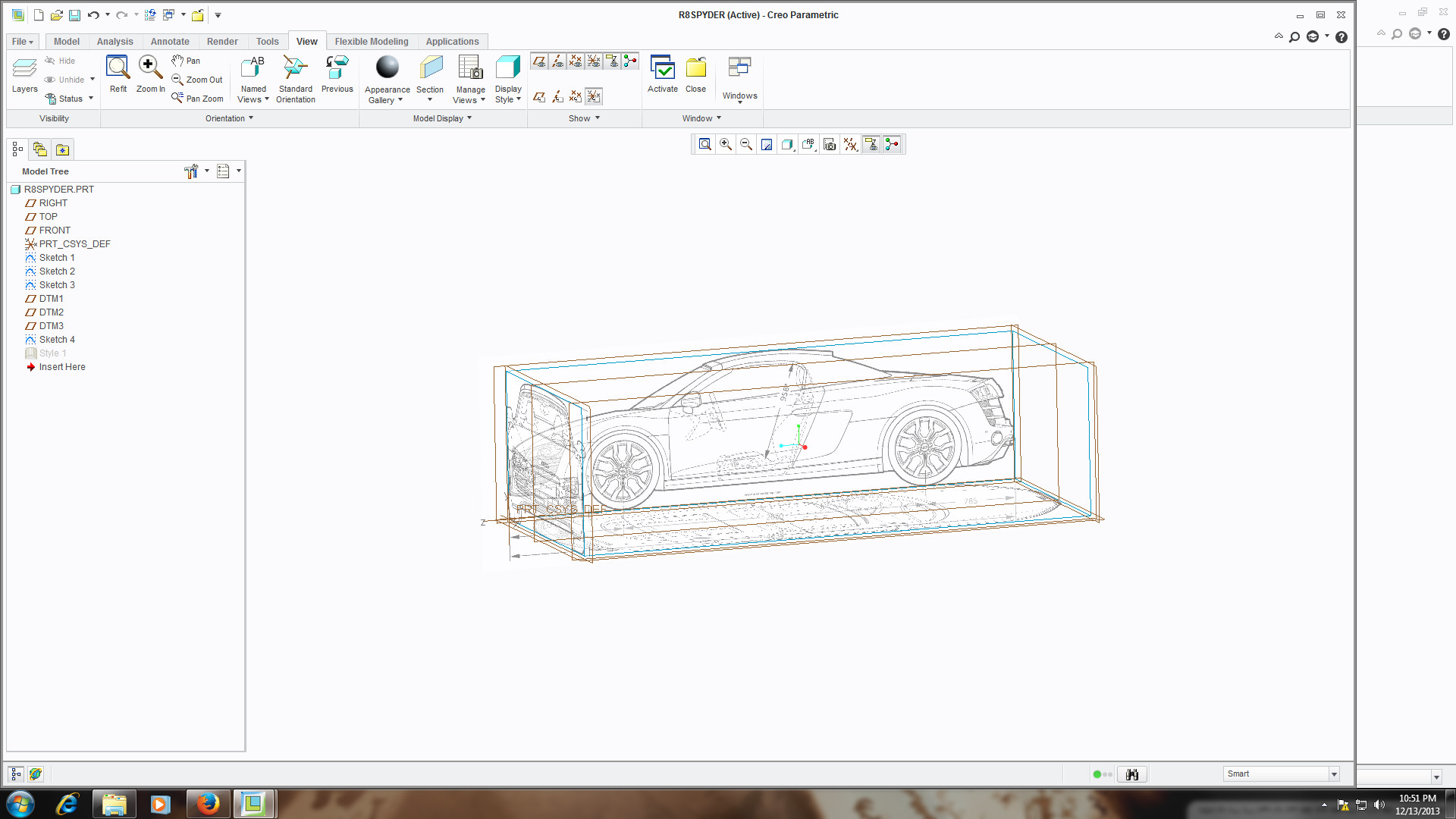
The requirement of a non-uniform mesh is a necessity and not a limitation.When you use the Spalart-Allmaras model or any other eddy-viscosity model with enhanced wall function, you should check that y + of the wall-adjacent cells is either very small (on the order of y + = 1), or y + ≥ 30.Both the frictional and pressure drag for bluff bodies is dependent upon extent of separation zones. Appropriate mesh sizing is critical because fidelity of local wall shear predictions affects the prediction of frictional drag for external flows or pressure drop (which is also a form of frictional drag) for internal flows. The mesh resolution near walls affect calculation of wall shear as well as separation zone and location of separation.However, hardware requirement (RAM, number of cores) increases with increase in no. Finer the mesh (lower the cell size), better is the result.

In general, the accuracy of CFD simulation is governed by cell size. The solution of flow problems are defined at nodes or face centres of the cells. The 2D boundaries of this smaller (discretized) domains are called Faces, the 1D boundaries are called Edges and 0-D boundaries are called Nodes or Vertices. This step involves division of the computational domain into small sub-divisions called a grid or mesh of cells/elements/control volumes. Have the inlet and outlet planes of a porous domain been assigned to separate internal patches? Have the walls been grouped into logical surface-groups easy to maintain during solution and post-processing? Have the areas of the boundaries been checked and matched with the values used to estimate boundary condition parameters? mf for mass-flow, vi for velocity inlets, po for pressure outlets. Have appropriate prefixes been added to the boundary names as per boundary type: e.g. Have the fluid and solid zones named as per material type say by adding air, ss, al, pl, cr (ceramics). Have sliver elements been collapsed? With minimum size ~ 0.05, elements having area < 0.002 or volume 0.0001 are unreasonable. Has the mesh quality been checked for skewness and aspect ratios (for boundary layers and for freestream elements)?
